Page 1 of 1
Instead of pouring Babbitt...
Posted: Thu Jun 18, 2020 12:24 pm
by Steve Jelf
Saw this on MTFCFB. What do you engine rebuilders think of it?
Re: Instead of pouring Babbitt...
Posted: Thu Jun 18, 2020 1:00 pm
by DanTreace
Looks like a bronze liner? Held with screwed down plates. One cap with liner shown in foreground with the crank. Don’t know if that’s good or bad.
More concern is no radius to the turned crankshaft journals.
Ford babbitt bearings last long enough for most T’s.
Re: Instead of pouring Babbitt...
Posted: Thu Jun 18, 2020 1:42 pm
by walber
How is oil supposed to get to the mains?
Re: Instead of pouring Babbitt...
Posted: Thu Jun 18, 2020 1:47 pm
by Mark Gregush
Oil pump to the caps maybe?
Re: Instead of pouring Babbitt...
Posted: Thu Jun 18, 2020 5:04 pm
by Scott_Conger
If the caps are babbited, it'd be very similar to a very early engine, which I believe, had cast iron bored-in-place bearing surfaces in the block. Not the longest lasting design.
On close inspection of the first picture, it looks as if the caps have bronze, too. If the caps are bronze, I don't think much of it at all, and without super-duper oil filtration, the crank is going to score pretty badly pretty quickly. The babbit digests all sort of junk, allowing it to embed harmlessly out of the way...not so with bronze. Bad idea.
Some Engineers are machinists, but very few machinists are Engineers. This is what you get when they think they are.
Re: Instead of pouring Babbitt...
Posted: Thu Jun 18, 2020 5:28 pm
by Scott_Conger
Yet another good reason not to sign up for FB.
And, makes me wonder why the Club would purposefully divide the hobby into two factions anyway... ;
Comment by Chris
The club has a sanctioned Facebook Page setup by me a long time ago. It only allows posts by club management.
https://www.facebook.com/modeltfordclub
The one mentioned above was setup by someone else.
Edit by Scott: Chris thank you so much for clarifying for me and undoubtedly others. It's use makes complete sense in an administrative mode. Again many thanks.
Re: Instead of pouring Babbitt...
Posted: Thu Jun 18, 2020 5:56 pm
by Henry K. Lee
I have to agree with Scott. Babbit is so forgiving. If you think triple gears take a hit, I do not believe under load that engine will last. The oil has to be so perfectly clean as stated by Scott in order for in to hold up.
My $ 0.03 worth,
Hank
Re: Instead of pouring Babbitt...
Posted: Thu Jun 18, 2020 6:33 pm
by Charlie B in N.J.
I'll tell you this: I sure as heck want to know more about this. I dumped FB quite a while ago so that avenue is out for me but I'm very interested as I consider having to send a block out for babbeting as a major expense and takes engine rebuilding out of my garage & my hands.
Re: Instead of pouring Babbitt...
Posted: Thu Jun 18, 2020 7:20 pm
by Allan
Charlie, I don't think that route would be any cheaper than a babbit job. First, the block and whatever caps are used will have to be accurately machined to accept the bronze liners. Then the liners would have to be machined to fit on their outside diameter. Then each liner needs to be locked in using the set screws and plates shown, once the plates are made. Once fitted, the whole would still likely have to be line bored.Then there still needs to be work done on lubrication methods/internal pipework. That's one heck of a lot of accurate machining/fabrication to be done.
From my memory, Dodge used such bronze bearing shells, but these were babbit lined so that in effect, one had replaceable babbit bearings.
Allan from down under.
Re: Instead of pouring Babbitt...
Posted: Thu Jun 18, 2020 7:36 pm
by Les Schubert
With a couple of thou of babbit on it I’m totally good with it. Of course I’ve done something effectively similar on a set of T rods and they are just fine with about.002-.003 of babbit!!
Re: Instead of pouring Babbitt...
Posted: Thu Jun 18, 2020 8:02 pm
by Kerry
With Les on this, good with it, would be better if it had a swipe of Babbitt on it.
The American Lafrance V12 engine had 1\4" thick Bronze replacement bearings as did many WW1 Europe aircraft engines, cars and trucks, and of coarse nothing new when it comes to steam engines and pumps etc, used and around long before Babbitt.
Re: Instead of pouring Babbitt...
Posted: Thu Jun 18, 2020 8:17 pm
by Henry K. Lee
Hey, Babbit washed bearings are a little different than bronze/brass bearings.
Re: Instead of pouring Babbitt...
Posted: Thu Jun 18, 2020 9:23 pm
by Scott_Conger
Kerry
to add to what you mentioned regarding early engines, for others thinking that reverting to 100 year old technology as an improvement, one thing the designer needs in any plain bearing, particularly in reciprocating bearings, are features of embedability, formability, and compatability with the material it is in contact with.
Bronze bearings were in a number of engines of the day, and as was found around WWII, SAE tested and found that those engines so equipped benefited from hardened crankshafts, resulting in more robust bearings (less damage to crankshafts). As a design, it's clear that bronze bearings in engines did not give way to babbit because babbit had a stronger lobby.
Les' solution is similar of course to insert bearings and in fact is an insert bearing. That babbit is performing a function.
That said, no one needs to avoid using uncoated lead/brass alloys in automobile engines because I said so. Defying good known engineering principles, and disregarding it's total relegation to history as a practical solution is no skin off my nose. Knowing what we know today, it's just stupid.
My heart goes out to that shop's customer. He has no idea what he is in for, and the shop better pray that the engine sees infrequent, easy use until out of warantee period.
One final note with regards to use in steam engines. First, the oil was a total loss system on reciprocating parts, constantly flushing out contaminants; embedability is far less important. Second, the lubricants were essentially boundary lubricant, not hydrodynamic lubricant, and babbit would not last at all on reciprocating joints under those conditions. Finally, steam expansion while extremely powerful, does not have the impact of an internal combustion engine, nor suffers from extreme pressures exerted during preignition which can occur with gasoline engines. In steam engines, tin/brass bearings were ideal, and frankly after all of these years, still is. Any comparison between steam and internal combustion engines' reciprocating bearings is comparing apples to oranges
Re: Instead of pouring Babbitt...
Posted: Fri Jun 19, 2020 1:18 am
by Steve Jelf
...makes me wonder why the Club would purposefully divide the hobby into two factions anyway...
Not sure I understand. We're way beyond two factions, if you want to call them that. There are two national/international clubs, MTFCA and MTFCI. Each has its own Facebook page. There are also several other Model T Facebook pages. Some are aimed at Model T folks everywhere, like Richard Goldman's MTFCFB, Mitch Taylor's Model T Enthusiasts, Jerome Hoffman's Model T Ford Owners, some are national (Argentina, Australia) and some are regional or local (Central Ohio, Southern Nevada, Southern Arizona). I see all of them as just more forums, like this, or Ford Barn, or Royce's site. This one is the best, especially for mechanical advice, but the others often have some interesting material as well.
Re: Instead of pouring Babbitt...
Posted: Fri Jun 19, 2020 2:30 am
by Kerry
Scott,
Calling it, reverting to 100 year old technology is one way of putting it but in saying 100 year old technology that still works today is another.
How may of us have pulled down modern engines that are running on the bronze/brass/ copper alloy of a slipper shall and the crank is still in spec for a new set, well I'd have to say over 50 years it as been many for me. Engines that run no filters, low oil pressure, poor servicing, high mileage and 3 times the rev range of a T.
Would I do it myself for a T engine? No because Babbitt work is easy for me.
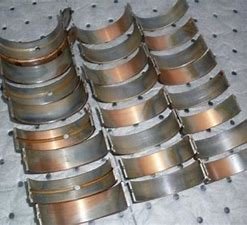
- OIPAPQW4S78.jpg (16.89 KiB) Viewed 10842 times
Re: Instead of pouring Babbitt...
Posted: Fri Jun 19, 2020 4:30 am
by Chris Barker
What is the MTFCFB please?
I even Googled it and got no answers
Re: Instead of pouring Babbitt...
Posted: Fri Jun 19, 2020 5:54 am
by Henry K. Lee
Model T Ford Club FaceBook
Re: Instead of pouring Babbitt...
Posted: Fri Jun 19, 2020 7:08 am
by Joe Bell
I have rebuilt two A's that had inserts in them that spun bearings out of them in less than three hundred miles,the problem was they did not run a filter system and it spun them out, some may like this ideal and it may work for some applications but I will stick to the Babbitt. Just my thoughts on this one!
Re: Instead of pouring Babbitt...
Posted: Fri Jun 19, 2020 8:32 am
by Jerry VanOoteghem
Kerry wrote: ↑Fri Jun 19, 2020 2:30 am
Scott,
Calling it, reverting to 100 year old technology is one way of putting it but in saying 100 year old technology that still works today is another.
How may of us have pulled down modern engines that are running on the bronze/brass/ copper alloy of a slipper shall and the crank is still in spec for a new set, well I'd have to say over 50 years it as been many for me. Engines that run no filters, low oil pressure, poor servicing, high mileage and 3 times the rev range of a T.
Would I do it myself for a T engine? No because Babbitt work is easy for me.
OIPAPQW4S78.jpg
Those engines you refer to were designed and engineered to work that way from new. Model T engines were not. Besides, I believe modern engines use hardened & nitrided crankshafts. Still, babbitted inserts, done well, should work, (as others have attested to from experience). In my case, my dad installed a bronze bushing in the the 4th main of my '21 Roadster. After 30K miles it was inspected and still had the .0015" clearance he made it to.
Re: Instead of pouring Babbitt...
Posted: Fri Jun 19, 2020 8:47 am
by John Warren
I think the bronze, not brass,bearings will be fine as long as they get lubricated, I am seriously considering installing bronze in my Maxwell 11AB engine. I am a rock crusher repairman, some of these crushers use all bronze bushings. The ones I have worked on for over twenty years run a minimum of forty hours a week and many run two 12 hr shifts 6 days a week! It was recently decided to rebuild these,( just because), and very little wear was found. No pinion shafts or spindle shafts ( the steel components that run directly against the bronze) needed replaced.The shafts and spindles are not hardened. These run with an oil pressure system at 20-30psi. The oil is easily contaminated, and usually is contaminated with dirt and water. The 400 horse power bushing crushers are amazingly forgiving. These crushers have so much belt tension on the pinion shafts that you can't turn them over by hand, even with the oil system running. Yes I think that wiping the bearings with babbit is a great idea. I'm not sure that they needed to install locking plates where a simple dowel would have worked. It appears that they are also running inserts in the rods. Something that is very important with the bushings is to have oil groves, hopefully they put some distribution groves in all their inserts, all of the crusher bushings have oil groves. On the Maxwell, one of the fixes for rods is to install model A rods, because they are lighter and better the way they bolt on the crankshaft. Maxwell's have a 1-3/8" journal and model A's have a 1-1/2" journal. So very thick babbit or some type of shell, and the main bearings are brass/bronze bushing though still babbit lined. Like Less, I think that the best oil system is a pressure system though my model a engine in my race car is running inserts with non pressurized mains and dip system for the rods ( stock oil system). The fellow ( Ron Kelly) that built my engine has engines with over 60,000 miles still running with no problems. I am very interested in how this works out, so keep us posted.
Re: Instead of pouring Babbitt...
Posted: Fri Jun 19, 2020 9:12 am
by Kerry
Jerry. That's the point about the posted question, A model T using bronze instead of conventional design or engineering. It worked before and after so really the question still remains on will it work for the T? We need an answer from someone who has done it before and give a result, just like your 4th bush, other wise we are working only on speculation and opinions.
Checked my engineering books and the min amount of Babbitt on building a shell of copper alloy/bronze crankshaft bearing is just .001 thou.
Re: Instead of pouring Babbitt...
Posted: Fri Jun 19, 2020 9:42 am
by Steve Jelf
Re: Instead of pouring Babbitt...
Posted: Fri Jun 19, 2020 10:01 am
by Scott_Conger
John
no one has mentioned using brass bearings. I have mentioned tin/brass (bronze). What bronze alloy will you use? How will it be finished? Do you know why the steel parts wore more than the bronze bearings in the rock crusher? In nearly every instance, where there is any possible source of contamination, the bronze will embed with particulate and the asperities will gleefully cut the steel to ribbons.
Before you commit your Maxwell's crank to a premature demise, do yourself a favor and do some study on bearing design and do not cut metal until you understand what Conformability, Embedability, and Compatability all mean with respect to bearing design.
Start reading here:
https://www.machinedesign.com/motors-dr ... als-part-2
augment that with this here:
https://www.machinedesign.com/motors-dr ... als-part-1
and that is just a start...
If you proceed with your plan, do tell the next owner what he is buying when you eventually sell the car. If he knows anything at all about bearing design, it will mean a great deal to him regarding the value of the car.
Jerry
I think that if there was a place that I'd put a bronze bearing where it wasn't designed to be, the 4th main would be the place. It's isolated from reciprocating forces and has a steady diet of a little clean grease and some dirty oil. That is the precise type of shaft and lubricant environment bronze bearings were historically alloyed and used for. Still, babbit is better suited in that location due to contaminants, and vendors do a very nice job and for less than I can install a bronze bearing, so will stick with original design. And due to the potential for flexing and minor misalignment at that location,I would personally use bronze or babbit before a ball bearing, to be sure.
Steve
by factions, I erroneously thought that the MTFCA had created a
SEPARATE MTFCA forum on another platform...that is what I meant by two factions. Chris has corrected my faulty thinking.
Re: Instead of pouring Babbitt...
Posted: Fri Jun 19, 2020 10:05 am
by J and M Machine
The bronze insert against the Model T Crank will be too hard and quick failure will result.
Where it's a splash rather than high pressure system the bearings and crank will not survive in the atmosphere of a Model T.
They chose babbitt because it's a softer material than bronze and it has ability to eat the dirt so as not to destroy the crank journal surface.
Modern insert bearings have micro layer of babbitt and have high pressure to wash debris away so that the crank rides on film of oil constantly.
In same situation if there were high pressure using a bronze bearing it still wouldn't have the ability to digest the fine debris that is always present in an engine. Note the picture; this is a rear main of a Model T that had been done by others and according to customer only had 10k miles on it.
See the amount of debris stuck in babbit, You can identify each piece, bronze, rust, glass beads. This engine had a Dubats crank in it and other than polishing crank would of been fine.
This is a testament of babbitt considering a poor engine rebuild the crank survived.
Re: Instead of pouring Babbitt...
Posted: Fri Jun 19, 2020 10:33 am
by Charlie B in N.J.
Nope. Not signing up for that again.
Re: Instead of pouring Babbitt...
Posted: Fri Jun 19, 2020 10:34 am
by Scott_Conger
Bronze worked before...that's true. And as a bearing for crankshafts and such, it (bronze) was abandoned. It is not speculation to state that the bronze will embed with particulates and slowly cut the steel to ribbons. The most successful early engines using bronze bearings also sported very hard crankshafts after designers came to this conclusion.
Those same particulates will also embed in babbit, but far further in, leaving fewer asperities protruding to cut the steel, and when pounded on, simply embed further, safely away from the bearing surface. It is not speculation or opinion. It is one of the natural features of a very lubricious material (babbit), which has made it so successful in so many applications for so many years. It has been supplanted by more modern materials in recent times, but typically in every one of those applications, superior filtering of the lubricant was provided for. The T was designed over 100 years ago, to run at about 1200 RPM for a few years and some (my opinion) ran for more than 30,000 miles over maybe 10 years. We on the other hand, run them flat out, well over designed RPM for many 10's of thousands of miles for sometimes 30+ years, all after they are 100 years old! I will reitterate for anyone who missed it before: it is just plain stupid to put bronze bearings on a crankshaft in a Model T or similar.
I am not the be-all and end-all for this subject, but did spend a career in precision lapping and honing, bearing design and gas-bearing manufacturing. If you want a good lap to cut even the hardest materials, the lap is the softer material. It is then embedded with desired compound, and much harder materials are lapped. One of the more interesting gas bearing gyros we made used Ferro-TCc material. It was a metal matrix of stainless steel with Titanium Carbide evenly dispursed. The aluminum lap flattened the material to 1 millionth of an inch flat, and then we gently polished the stainless back, leaving islands of super-flat TiC. It was an extrordinary example to new engineers in the ability for a prepared soft metal to cut away one of the hardest materials there is.
The softer the material, like lead or tin, the shorter the time the lap is useful, as the particulate continues to embed and ceases to cut. Brass, bronze and aluminum are much better at lapping things because the particulate stays trapped on the material's surface and will cut like crazy until the particulate is literally worn out. The old boys knew this and wrote books about it. Folks today are too smart to read those books, and claim that the ones who really know are just sporting "opinion". I know this because most everyone I worked with were far smarter than me, but in the end accomplished very little in their career other than making sure everyone knew how smart they were. I spend my time either in the shop or the clean room using time proven methods on new materials and developed a number of successful products and processes which have been in production now for over 20 years in the guided missle business.
Re: Instead of pouring Babbitt...
Posted: Fri Jun 19, 2020 12:05 pm
by Les Schubert
I could understand going to the effort of the thin babbit bronze liner on the main caps because that is where the bulk of the bearing load is. When I did my thin babbit bronze liner rods it was just on the rod itself and the caps are just babbitted like usual because again that is where the bulk of the load is.
Just my thoughts
Re: Instead of pouring Babbitt...
Posted: Fri Jun 19, 2020 1:48 pm
by Corey Walker
Here are some pictures of a motor I bought that had a bronze 1/2 bearing on the center main as part of a device to take up end play.
Re: Instead of pouring Babbitt...
Posted: Sun Jun 21, 2020 1:37 pm
by Gene_French
Have read this post with some interest … and while this type of machining to install insert bearings is certainly doable , I would have to ask why ? the bronze in itself is not a good application in the case of Model T , and the required machining is WAY in excess of the work required in re-babbitting and lineboring the block as original ...I would estimate that the required machining would take 3 to 4 times as long as re-babbitting and the bronze insert without a Babbitt lining would suffer all the issues described in detail in previous posts … a lot like COMPLICATING a HOTDOG … I do manufacture the tooling to re-Babbitt Model T , and the shipping on this tooling is way less than the shipping on a motor block , caps and crankshaft … that is my self promotion for this day ...always an optimist Gene French
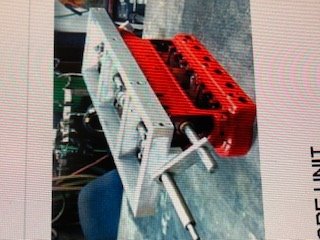
- linebore1.jpg (26.41 KiB) Viewed 10296 times
Re: Instead of pouring Babbitt...
Posted: Sun Jun 21, 2020 6:03 pm
by Susanne
Corey Walker wrote: ↑Fri Jun 19, 2020 1:48 pm
Here are some pictures of a motor I bought that had a bronze 1/2 bearing on the center main as part of a device to take up end play.
That crank looks beefier than a stock Ford...
I'm waiting for a set of main bearing caps to arrive, then to start the long and ardupus process of refitting the block to take a Wills St. Claire crank... since it's a pressure oil crank anyway, and I'll have to do the work to fit it's huge journals to a T block. I'm going to fit bearing shells and filtration (as did Wills back in the day) and (fortunately) have a pulley driven oil pump (currently on the bench) and brackets. Of course, then there's the conrods to deal with... Someone said tubular rods, another said have Scat make a set forged to fit...
I keep thinking there's an easier way to do this, and what did I get myself into... but then it wouldn't be as fun. I think. Maybe?

Re: Instead of pouring Babbitt...
Posted: Thu Jun 25, 2020 9:13 am
by John Warren
Something that I wanted to add this post is, Most everyone that has had a model t engine apart will find that the rear main ( next to the flywheel) will have crap embedded into it. If you wonder why it, is usually the only one with the crap embedded in it, It is because it gets half of its oil from the transmission. During my engine rebuilds, I plug the oil hole off on the transmission side so it only gets oil from the engine side. This keeps fragments from the transmission/starter,bands etc from just running in to the oil port feeding the rear main. Thousands of miles and no issues with the rear main bearing, so it must still be getting enough oil with that hole plugged. Just a thought!
Re: Instead of pouring Babbitt...
Posted: Fri Jun 26, 2020 10:36 am
by Les Schubert
John
I like your idea!! And considering that my experience is that the centre main wears the most I now drill two holes for it
Re: Instead of pouring Babbitt...
Posted: Fri Jun 26, 2020 5:43 pm
by Kerry
John.
Maybe USA blocks? have a oil hole on the fly wheel side of the main but Canadian ones don't.
Re: Instead of pouring Babbitt...
Posted: Fri Jun 26, 2020 6:38 pm
by Scott_Conger
Kerry
thanks for sharing that. A fact that I did not know.
Re: Instead of pouring Babbitt...
Posted: Fri Jun 26, 2020 7:13 pm
by Les Schubert
I’ve seen Canadian blocks both ways
Re: Instead of pouring Babbitt...
Posted: Fri Jun 26, 2020 7:31 pm
by Kerry
Just checked. Out of a dozen blocks I have, teens and through the 20's, yes one was, a 1926, In that the blocks came to Canada up to late 1917/early18 from the USA, made me wonder on how much machining etc Canada did. If USA was using that oil hole in the teens then Canada must have done everything on a blank casting. A 1913 and some 16'ns I have, no oil holes.