Page 1 of 1
blown head gasket(s)
Posted: Wed May 26, 2021 4:27 pm
by bobt
Hello. I've owned my 1926 roadster for about two years now and I am replacing the second head gasket that has blown in the same place after about 11 months. The engine has a lot of upgrades that were done by the previous owner. I know it has aluminum pistons,plus an aluminum Z head, Bosch distributor, sure stop disk brakes and the like. The head gaskets are blowing at the thinnest area between #one and #two cylinders. I'm planing on having the head milled and replace the gasket with the standard copper fiber sandwiched one. The book says that the new improved gasket can't be used with a Z head. Yes, I am running with TWO zinc anodes. Any comments or ideas ? Thanks, bobt
Re: blown head gasket(s)
Posted: Wed May 26, 2021 4:36 pm
by Norman Kling
If the top of the block and the bottom of the head are straight, any T gasket should hold if you follow the diagram for torquing the head to 50 ft lbs. I have read where use of a copper gasket can cause electrolysis.
Norm
Re: blown head gasket(s)
Posted: Wed May 26, 2021 5:01 pm
by paulgriesse
I had a similar problem with an old (early) Z head--------between #1 and #2 Clys. Milling it down helped but I noted my later Z head was visibly thicker at that location and I`ve run it with no gasket problems on one of my Ts----Thanks, Paul
Re: blown head gasket(s)
Posted: Wed May 26, 2021 5:13 pm
by Rich Eagle
Make sure the bolt heads are tightening on the head. If they bottom out in the holes they will not make contact with the head. Milling the head will make that problem worse. Old bolts can stretch over the years. I had this problem one time.
Rich
Re: blown head gasket(s)
Posted: Wed May 26, 2021 5:34 pm
by speedytinc
Old racer trick. Place a thin copper wire between the cyls. under the head gasket.
Re: blown head gasket(s)
Posted: Wed May 26, 2021 5:54 pm
by Joe Bell
When you torque the head to 50 ft.lbs. run it till warm, shut it down let cool, next day retorque to 50 lbs again, run it till warm shut it down to cool off next day retorque again, this all sounds like a waist of time but they will move, also use new bolts the old bolts stretch at about 50lbs. make sure you also use the stainless washer for the aluminum head. Hope this helps, been here done this many times!
Re: blown head gasket(s)
Posted: Wed May 26, 2021 6:00 pm
by Henry K. Lee
Exactly what I do Joe.
Hank
Re: blown head gasket(s)
Posted: Wed May 26, 2021 8:39 pm
by Art M
Even with a cast iron head I always retorque the head bolts several times after engine is run. Torque the manifold bolts as well.
Joe, why stainless steel washers with the head bolts instead of just plain steel washers.
Art Mirtes
Re: blown head gasket(s)
Posted: Wed May 26, 2021 9:03 pm
by TXGOAT2
Stainless washers are hard and "slick". The bolt heads will not cut into them and they will allow more accurate torque readings. If the bolt bosses on your aluminum head are chewed up, they need to be milled off smooth. If that is the case, be sure the head bolts aren't bottoming in the block. they may need to be shortened slightly. Any dirt in the bolt holes will cause problems, and anything done to the head or block as far as resurfacing will raise the possibility of the head bolts bottoming, even in clean holes with good threads.
Re: blown head gasket(s)
Posted: Wed May 26, 2021 9:07 pm
by jiminbartow
As the diagram says. Do not tighten all at once. Go around several times, tightening a little at a time, evenly, five times or so in the order indicated by the numbers. The last time, torque to 50lbs. Be sure to use a spray on copper gasket sealant on both sides of the copper head gasket. Jim Patrick
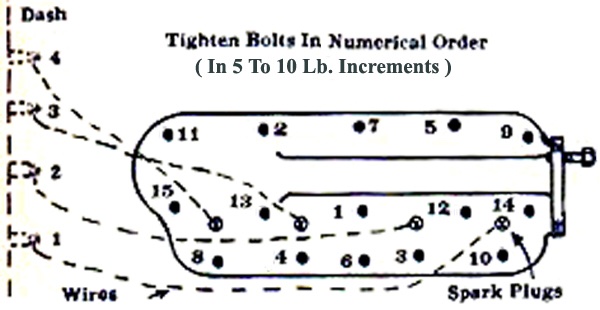
- 14370954-0C4B-4FDC-9387-3E809B666794.jpeg (73.38 KiB) Viewed 3855 times
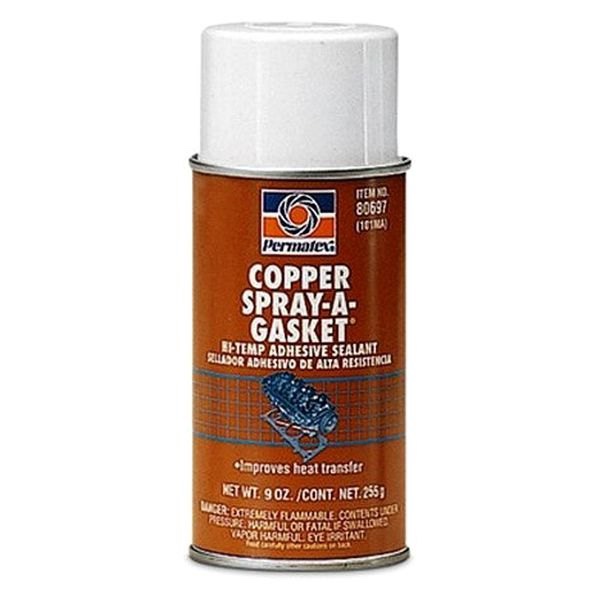
- 729C99DE-0C09-416C-83DC-FD4E84E1DDAC.jpeg (59.96 KiB) Viewed 3855 times
Re: blown head gasket(s)
Posted: Thu May 27, 2021 9:48 am
by DanTreace
The
proper sequence is needed for the Ford cylinder head bolt tightening. The
center bolts must be tightened down first. This is because the head gasket is so narrow between cylinders 1-2 and 3-4. And for best results of a long living gasket, the cylinder head and block surface should be flat, preferably surfaced to be totally level.
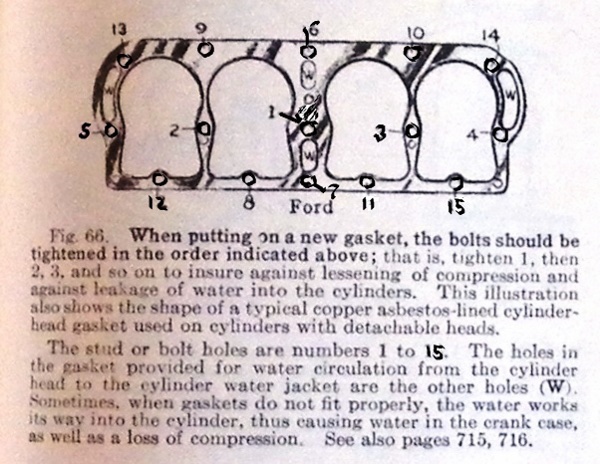
- fg84 (600x464) (2).jpg (153.49 KiB) Viewed 3726 times
As others posted, test the bolt lengths in the block holes, be sure they are clear of debris to the bottom of each hole. A bolt bottoming out will strip the threads in the block quickly.
Ford Service Manual,
center bolts torqued first.
Re: blown head gasket(s)
Posted: Thu May 27, 2021 10:39 am
by Cordes_jeff
Have you put a straight edge across the block to see if it is flat. You may have a low spot on the deck which will blow a gasket every time.
Re: blown head gasket(s)
Posted: Thu May 27, 2021 10:50 am
by Norman Kling
Well! I've seen at least 4 "proper" sequence diagrams. Most important is to start in the center and work out, tightening a few foot lbs at a time until you reach 50. Then warm up the engine without driving it. re-torque to 50 while hot if the iron head, but if aluminum, wait for it to cool down before you re-torque it. Then start it up and drive a short distance maybe a mile or two just enough to get it to normal operating temperature. Repeat the torque process either hot for iron head or cold for aluminum head. Do this at least one more time until it remains at 50 after you have driven it.
Norm
Re: blown head gasket(s)
Posted: Thu May 27, 2021 11:08 am
by Adam
TXGOAT2 wrote: ↑Wed May 26, 2021 9:03 pm
Be sure the head bolts aren't bottoming in the block. they may need to be shortened slightly. Any dirt in the bolt holes will cause problems, and anything done to the head or block as far as resurfacing will raise the possibility of the head bolts bottoming, even in clean holes with good threads.
8 posts here before someone was experienced enough to NAIL THE MOST LIKELY CAUSE!
In 18 years of doing T service work on a fairly full time basis, the ONLY bona-fide cause for “leaking or blown” head gaskets I ever saw was issues with the bolts being too long or not properly bottoming against the head because of dirt/carbon in the bottom of the holes. I saw a couple other issues caused by gasket coatings and various other degrees of benign ignorance, but 19 times out of 20, it WILL BE the bolts aren’t torquing against the head!
FYI... There have been a couple runs of head bolts from some of the major vendors within the last 30 years or so that ARE a bit too long. It is one of the many known issues to watch for amongst the people who do a lot of T service work and engine building.
Re: blown head gasket(s)
Posted: Thu May 27, 2021 11:55 am
by Steve Jelf
Well! I've seen at least 4 "proper" sequence diagrams.
It seems there are almost as many different diagrams as there are timers or spark plugs. Most of them follow the Service Manual recommendation Dan posted.
This is the one that comes with the instructions for the MT-100 gasket.
Re: blown head gasket(s)
Posted: Thu May 27, 2021 1:46 pm
by TXGOAT2
I'd torque heads with a "sandwich" type gasket in 3 or 4 progrssive steps, following the recommended pattern and sequence with each step. When all bolts are at full recommended torque, run the engine to operating temperature and then retorque as needed. I do that several times. Follow any manufacturer's instructions with an aluminum head or specialized gasket, such as running to operating temperature and allowing cool down, then retorquing. Some modern engines do not require retorquing heads, but Most early engines do. Model T engines definitely do, as do Model As and V-8s. Some Ford flatheads have over twenty head bolts (or nuts) ... X 2.