Page 1 of 1
Steel vs Iron
Posted: Tue Aug 23, 2022 1:42 pm
by schwabd1
OK, I'm far from a metallurgist...... How do you tell cast iron from cast steel? I'm guessing intake manifolds are cast iron. I want to make a "custom" intake based on parts from an original intake, so I'll need to do some welding / brazing.
Re: Steel vs Iron
Posted: Tue Aug 23, 2022 2:05 pm
by TXGOAT2
Cast iron is what the block, head, and intake and exhaust are made of. It has a characteristic "grainy" surface and is usually somewhat irregular except where it has been machined. It is used where strong, stiff parts with complex shapes are needed. Forged steel can resemble cast iron, but forged parts have their own typical surface finish and are usually thinner, lighter parts used where light weight and very high strength are needed. Compare the front axle and spring perches on a T to the block and cylinder head. Cast steel is not commony used. Cast steel parts are usually have smoother surfaces than cast iron, and they are used where light weight and high strength are required. Sheet steel can be formed into almost any shape, and usually has a smooth surface. Fenders, exhaust pipes, T oil pans, and such are made of sheet steel. Forgings can be bent, given enough force. Cast iron will fracture under stress. Sheet steel will bend, stretch, tear, or crumple. Cast steel is somewhat malleable. Cast iron is poured into molds as a liquid. Forged parts are forced into shape using hammers and dies. Sheet steel is rolled into sheets of the required thickness, then cut and shaped as needed. Stamped steel parts are formed in somewhat the same way as forged stel items, but the process is quite different in practice. Most all parts made of iron and steel require a number of steps to form, then a number of additional steps, such as machining to final dimensions, drilling and tapping, punching, riviting, heat-treating,, etc. to finish the item.
Re: Steel vs Iron
Posted: Tue Aug 23, 2022 2:14 pm
by TXGOAT2
It can be very difficult to weld or braze cast iron. Very difficult. Cast iron is brittle, it is of uncertain formulation; it expands a great deal when heated to welding/brazing temperatures, and is very prone to crack when cooling and shrinking after welding/brazing. Most castings have some impurities in them, and may have air bubbles, sand pockets, scale, sand scabs, oil, or other contaminants, not to mention corrosion. Most castings have non-uniform section thickness, which complicates control of heat and shrinkage. Old castings often have micro-cracks in them. Unless you have a lot of experience working with old cast iron, and the right equipment on hand, you'd best do lot of reading, and a lort of practicing on junk castings before you work on anything you want to keep.
Re: Steel vs Iron
Posted: Tue Aug 23, 2022 2:43 pm
by speedytinc
schwabd1 wrote: ↑Tue Aug 23, 2022 1:42 pm
OK, I'm far from a metallurgist...... How do you tell cast iron from cast steel? I'm guessing intake manifolds are cast iron. I want to make a "custom" intake based on parts from an original intake, so I'll need to do some welding / brazing.
I have had good luck brazing cast iron. Cool slowly by backing off the torch heat until all the red is gone.
See dual NH carb setup. The intake was made from 2 stock intake manifolds brazed.
Re: Steel vs Iron
Posted: Tue Aug 23, 2022 4:32 pm
by Craig Leach
Hi David,
What did you have in mind? I have seen & welded some manifolds, The first T manifold I welded I tacked a steel flange on so & could braze it. I didn't get it straight so I went to knock it off with a hammer & found it didn't come off easy. When I got it tacked on straight I wormed it up & welded it with the wire feed and cooled it very slowly in a bucket of floor dry ran it for years before I switched to a up draft that was much smaller ( WF Carter is over kill for a stock T ) The rusty up draft manifold was on a engine I picked up that had 6" straight pipes, low head & the pistons & rods where drilled to reduce weight. It was brazed & appears to have held up well.
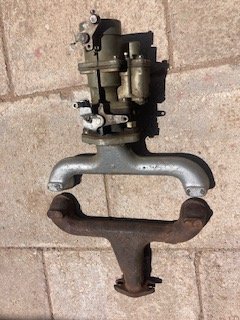
- manifolds.jpg (25.34 KiB) Viewed 1752 times
I think that T intake manifolds are made of very good grade castings.
Craig.
Re: Steel vs Iron
Posted: Tue Aug 23, 2022 9:36 pm
by Wayne Sheldon
So many variables to consider. Pig iron, wrought iron, nearly all cast "iron" is technically a "steel" of some sort. It all depends upon the particular alloy mixtures, and the quality of the mix. Cast iron varies so much, that many items cannot be welded if they are on the tail end of a "pour", while earlier items can be welded with ease.
For whatever it is worth, I have welded and/or brazed a number of Ford intake manifolds. They have always responded well. Exhaust manifolds are often a different story (often due to the difference in the iron due to expected high heat).
I once built a custom intake manifold by brazing cut up cast iron pipe fittings into the complicated shape I needed. It looked and worked great for the several years I drove that car a lot!
Re: Steel vs Iron
Posted: Tue Aug 23, 2022 9:47 pm
by TXGOAT2
"Black" low pressure NPT pipe fittings are malleable iron, which is a sort of semi-steel. Forged steel pipe fittings are available at extra cost. Low pressure SS fittings are the same pattern as black malleable fittings. Aluminum electrical conduit fittings may be available in aluminum. I ran into some 4" stainless electrical conduit fittings that looked like NPT, but they had straight threads. We had to have the joints welded to get them to hold water under high pressure. Forged steel weld fittings are available also. They typically have nice smooth bends and curves. McMaster Carr probably has every kind of pipe and tubing fitting ever made.
Re: Steel vs Iron
Posted: Wed Aug 24, 2022 9:49 am
by George Mills
David,
Chances are that manifold is in fact Cast Iron. Old school foundry methods of the era allowed cast iron to be pulled from the sand within 24 hours, often next shift, shaken down and sent off for machining immediately. (perhaps not too bright on this last one, but hey...it worked, most of the time and a good foundry man of the old era knew how to prevent blow-holes from the second run of a pattern). Today, this process is even faster as tempering tunnels and shake tunnels are engineered to run at the same speed as the core boxes run under the spigot. There are even ways today to liquify any captured sand and have it 'melt' away to be recycled, so that at the exit of the tunnels the castings are ready to be de-flashed while still 'warm'.
Old school cast steel of the era had the pour occur, then MORE sand added as a cover-over, then allowed to self temper in the sand until room temperature to prevent 'spring' at release. Economics of the time probably favored cast iron almost universally. Tying up a pouring bay for over a week doing cast steel would have been horrendous. Not impossible, but not too smart.
They only way to tell at home is to do the old spark color test. Best to video then rewind and watch. Find an area where grinding wheel bruise/hickey won't matter. Hit it quick to throw a spark pattern. Yellow sparks are indicative of Steel. Low glow orange/red indicative of Cast Iron. Some guys claim they can tell by the spark spray pattern...I can't and have tried many times over the years, but I've never thought of videoing before...