Page 1 of 1
sediment bulb screen - what's the trick ?
Posted: Tue Apr 28, 2020 8:38 pm
by Wayfarer
I need advice / tips / tricks for soldering the screen on the sediment bulb outlet.
cap is bead blasted and the edge is filed clean and shiny, but I can't get the solder to flow.
what solder are you guys using ? flux ?
what heating tool are you using ?
I've sweated copper pipes before, and I can solder electrical connections and wires, I've even done a little lead body filler, but this is NOT working !
Re: sediment bulb screen - what's the trick ?
Posted: Tue Apr 28, 2020 8:48 pm
by KWTownsend
Cory-
I have heard that even with the proper flux, "new" solder is not as user friendly as old solder and may be resistant to flow on cast iron and steel.
This might be a job for JB Weld.
: ^ )
Re: sediment bulb screen - what's the trick ?
Posted: Tue Apr 28, 2020 8:53 pm
by TRDxB2
I'd use something like Permatex Permashield Fuel Resistant Gasket Dressing & Sealant. Makes it easy to replace later.
Re: sediment bulb screen - what's the trick ?
Posted: Tue Apr 28, 2020 8:55 pm
by John kuehn
This is another one of those ‘how did Ford do it’. I’ve did it but it wasn’t a smooth as the original. Seems like I used solder that was used in Refrigeration work that had a good content of silver.
Re: sediment bulb screen - what's the trick ?
Posted: Tue Apr 28, 2020 9:04 pm
by DanTreace
Have used my old well-worn Wren 100w soldering gun, worked ok. Solid core solder. Used paste flux on cleaned with lacquer thinner edges of the screen nut.
Then tinned the screen nut surface, while hot placed the new screen. Then applied solder to the outer surface, the pre-tinned edges allow the solder to weep good into the tiny screen opening, layer on more solder and smooth along the way with the hot gun tip. Looks messy, but is on there and sealed.
Try to keep solder off the threads of the nut, but easy to file away the excess that gets in there anyway
Re: sediment bulb screen - what's the trick ?
Posted: Tue Apr 28, 2020 9:08 pm
by Rich Eagle
Re: sediment bulb screen - what's the trick ?
Posted: Tue Apr 28, 2020 10:24 pm
by Wayfarer
got it !
definitely not my best work.
I ended up preheating with my butane soldering torch, then paste flux, then wide soldering tip, sort of "puttied" a solder ring on the cap.
laid screen on, then put the wide soldering tip down on top of the screen, and kind of "puttied" all the way around, only had to add a little solder in a couple spots.
should've taken a picture, I got too excited and already put it back on the sediment bulb
Re: sediment bulb screen - what's the trick ?
Posted: Wed Apr 29, 2020 10:27 pm
by Mike Thomas
Clean the bulb, add flux, use a torch to heat the bulb, and get the solder to stick to the flange. Get a little bead of solder stuck there. Let things cool. Lay the screen on the bulb and heat the bulb from underneath. If you get the flame/heat too close to the screen it will melt. Just heat the bulb until the screen 'falls' into the molten solder. Works every time....
Re: sediment bulb screen - what's the trick ?
Posted: Thu Apr 30, 2020 1:48 pm
by richc
Thanks to everyone for posting their soldering advice. I learned some good ideas. It didn't do the pre-tinning, but still ended with satisfactory results. Remember when soldering, "Cleanliness is next to Godliness."
Rich C.
Re: sediment bulb screen - what's the trick ?
Posted: Thu Apr 30, 2020 3:41 pm
by Quickm007
Personally I used this paste with successful. Still working after 15 years...
Re: sediment bulb screen - what's the trick ?
Posted: Thu Apr 30, 2020 3:59 pm
by Jerry VanOoteghem
This is no place for a soldering gun. You need a torch to give enough heat to heat the brass so that the solder melts when placed in contact with the brass. First rule of soldering, (well, maybe the second rule, behind cleanliness), is to apply heat to the part and not to the solder. Let the part heat the solder, otherwise you get a "cold joint", which has no strength. If you don't have an adequate torch, place the cap on a gas stove with a low heat. Heat until touching the solder to the joint results in the solder flowing.
Re: sediment bulb screen - what's the trick ?
Posted: Thu Apr 30, 2020 5:09 pm
by Wayfarer
my cap is iron, not brass
I used a propane torch at first, and then switched to my butane torch, and then to my butane torch with wide flat soldering tip. so...preheat, then preheat, then localized heat
getting the solder to melt wasn't my problem. getting it to stick was my problem. possibly a flux issue ? I tried two different fluxes, the second one worked...begrudgingly
I started with a bead blasted cap, then filed it, then sandpapered it
Re: sediment bulb screen - what's the trick ?
Posted: Thu Apr 30, 2020 5:38 pm
by John kuehn
Looks pretty good. I’m thinking that when these were put together at Ford the guys doing the soldering had a certain method and some type of jig set up to solder the screen in. However they did it they got pretty good at it. Practice makes perfect and they certainly got a lot of practice doing it in mass production!
Re: sediment bulb screen - what's the trick ?
Posted: Thu Apr 30, 2020 9:11 pm
by Jerry VanOoteghem
wayfarer wrote: ↑Thu Apr 30, 2020 5:09 pm
my cap is iron, not brass
I used a propane torch at first, and then switched to my butane torch, and then to my butane torch with wide flat soldering tip. so...preheat, then preheat, then localized heat
getting the solder to melt wasn't my problem. getting it to stick was my problem. possibly a flux issue ? I tried two different fluxes, the second one worked...begrudgingly
I started with a bead blasted cap, then filed it, then sandpapered it
I missed the cast iron versus brass part. Yup, that's a bit more difficult. Even when the surface is clean cast iron can absorb "stuff" that can leech out when heated. Sounds like you've got it licked!
Re: sediment bulb screen - what's the trick ?
Posted: Fri May 01, 2020 1:33 am
by TRDxB2
No one mentioned the type of solder they were using . Not all "solder" has the same melting point - a KESTER chart shows from 291Farenheit/144 Centigrade to 574F/301C depending on the proportion of Lead and Tin sometimes Silver or Bismuth. Besides the wire form there is also solder paste composed of flux and solder balls that is used on circuit boards and common for the melting point to be at 290F. Wondering if this thick concoction was used back then - would make the assembly much easier.
Re: sediment bulb screen - what's the trick ?
Posted: Fri May 01, 2020 2:25 pm
by Wayfarer
Jerry VanOoteghem wrote: ↑Thu Apr 30, 2020 9:11 pm
wayfarer wrote: ↑Thu Apr 30, 2020 5:09 pm
my cap is iron, not brass
I used a propane torch at first, and then switched to my butane torch, and then to my butane torch with wide flat soldering tip. so...preheat, then preheat, then localized heat
getting the solder to melt wasn't my problem. getting it to stick was my problem. possibly a flux issue ? I tried two different fluxes, the second one worked...begrudgingly
I started with a bead blasted cap, then filed it, then sandpapered it
I missed the cast iron versus brass part. Yup, that's a bit more difficult. Even when the surface is clean cast iron can absorb "stuff" that can leech out when heated. Sounds like you've got it licked!
it's on there, and while it's not my best work, it WILL work.
TRDxB2 - this is where I'd like to get more feedback. What solder ARE people using / having success with. ? Silver solder ? 60 / 40 ? And perhaps flux brand name / type as well.
I'd sure like to have an easier time next time !
Re: sediment bulb screen - what's the trick ?
Posted: Fri May 01, 2020 2:42 pm
by Scott_Conger
Eutectic solder, 63/37, good flux, pre-tinned parts (thoroughly, shiny, no voids), and then sweat them together with just a dab more solder. Do not heat the solder...heat the part.
If you use an iron, use
250W and maintain a
good solder bridge during tinning, and the reflow when attaching the screen. A torch can be used, but you're heating the entire part and losing control of the entire process. If you have the proper iron, you may wish to have a helper keep the body warm with the torch so as to aid the iron.
Iron:
https://stellartechnical.com/products/a3158x-250w-iron
I have one of these irons and use a standard household dimmer switch and an electical outlet in a HandiBox to keep the heat at the tip at the right level based on the work load. This sort of setup is common for anyone working on starters or similar heavy copper buss soldering. You get in quick, apply the right heat to the right spot and get out before the entire assembly heats and scorches. If you do not own one, you don't know how handy it is.
Re: sediment bulb screen - what's the trick ?
Posted: Fri May 01, 2020 5:00 pm
by HornsRus
i learned this from an old rad man,he sandblasted everything before hand.it works well espley on cast iron.charley
Re: sediment bulb screen - what's the trick ?
Posted: Fri May 01, 2020 6:30 pm
by Scott_Conger
Charley
that was and is good advice. It's all about removing oxides from the surface to be soldered. Soldering should follow immediately after blasting and cleaning as oxides begin building up pretty much immediately. There is only so much that flux can do.
Good that you mentioned this.
Re: sediment bulb screen - what's the trick ?
Posted: Mon May 11, 2020 8:55 pm
by TRDxB2
After reading this discussion I thought I'd take a shot a replacing the screen in a bulb I have. As I was pulling the old screen out I was surprised to see that it was held in place by a collar of brass folded over it. Maybe after cutting the threads the left a thin collar while machining out the inner surface to it could be folded over the mash. I put a fitting on the end of the screen cover so it would sit up from the vise jaws. I pried the collar up a bit with a utility knife blade by tapping it gently all the way around. When it appeared to move no more I quit.
Next wire brushed the entire surface.
A touch of flux I had laying around from the 1980's. Heated the cover from the bottom (Jerry's stove idea) with a propane source and when hot melted a bead of 50/50 solder around the edge.
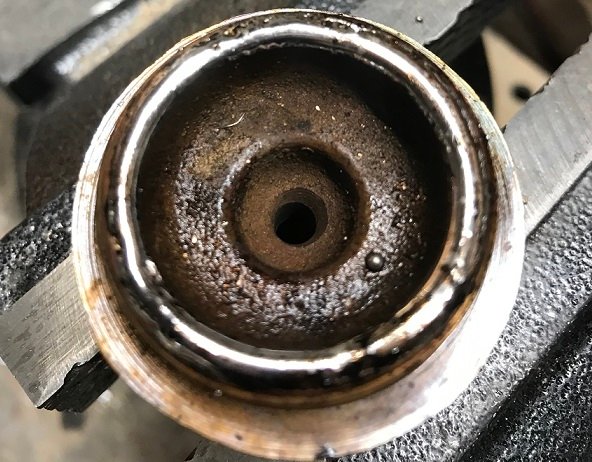
- 3 solder.jpg (89.97 KiB) Viewed 6669 times
The mesh was slightly waffled like a spring washer (hindsight says I should have domed it). Rolled the edge of the mesh through a bit of flux and placed on top of the solder
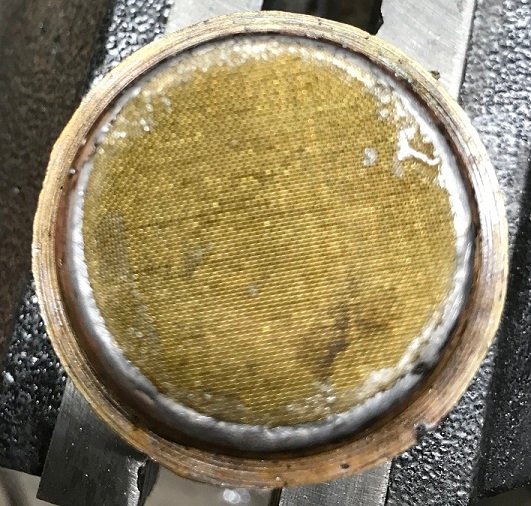
- 4 lay up.jpg (97.86 KiB) Viewed 6669 times
To keep the mesh in place and to prevent it from melting I put a bolt on top of it. Re-flowed and let the mesh settle into the solder
Re: sediment bulb screen - what's the trick ?
Posted: Mon May 11, 2020 8:57 pm
by TRDxB2
Done - still learning